在本文中,我们将汇总并解答人们面临的五个最典型的误解。
1. “我很满意目前的设备利用率,因此我不需要自动化。”
我们最好借助数据来看待这一观点。比方说:在过去一段时间内,您的机床实际的主轴切削时间是多少?如果机床仅仅是单机运行,且每台机床配有一名操作员,就会导致大量的时间消耗在:
- 人工设置
- 夜班和周末无人
- 意外事件:如故障排查或新插订单
但在实际情况中,以下问题也会经常出现,造成更多的时间浪费:
- 在开始新批量生产前,由于原材料或刀具的缺失导致的延误
- 非标准化生产工艺导致的延迟或报废
可能您从未测量过机床的利用率,这便意味着您并不掌握真实的数据,也就根本谈不上对工作效率的进一步提升。
那么下一步,我们必须了解这些数据是如何被测量的。有时,制造商们声称他们的机床在做生产设置时也被认为机床在工作,然而矛盾点在于,“在这段期间内,机床根本无法工作”。这是一个事实,但是经常被误解。”。事实上,单机最大利用率仅为45%,平均水平在30%左右,当然,您可以决定这样的利用率是否满意,但以下是我们的看法:
每一年都有8,760小时,我们能做到的就是尽可能充分地利用这些时间。凭借智能自动化解决方案,Fastems可以帮助企业达到年8,000小时(90%以上的机床利用率)的实际生产时间。既然如此,您还会满足于30-40%的利用率吗?或者进一步思考,如果能够将您的设备利用率翻倍,这会对您的竞争力及产能起到哪些积极的作用?
2. “我们产量少,使用自动化不合适。”
这种说法我们在许多行业展会中经常听到。人们对此有一种普遍的误解,即认为自动化只适用于那些产量从几十万到几百万的制造商——比如汽车行业。
真相在于自动化的类型:对于批量为1-5件的生产来说,利用自动化也是可以达到经济生产的目的,但它需要的系统不同于私家车制造的刚性自动化系统。看下我们的案例就知道了,像Kempf和苏州新鸿基等中小型企业或我们的一些其他做代加工的客户。事实上,我们大多数的客户生产的批量小,品种为几十至数百或数千种,这正是智能柔性自动化的优势。
那么,经济型小批量生产和自动化的关键因素是什么呢?以下我们提供了两大关键因素:
- 在生产过程中,换型必须高效快速。Fastems的FMS(柔性制造系统)和机器人单元——Fastems敏捷制造单元——配备先进的夹爪技术和控制软件。
- 先进的生产计划管理软件,能够控制并保障生产的顺畅进行,同时也能最大限度降低因资源缺失和临时生产变更造成的时间损失。
不论批量大小,都可以实现自动化。在Fastems的众多成功案例中,有一些客户的生产批量只有一件——结果证明经济可行。
3. “自动化太难了。”
自动化时常被认为是既复杂又充满风险——只有拿到博士学位的人才能理解。几十年前或许是这样的,而如今,任何制造商都可以使用自动化,并通过学习不断改进生产效率。使用自动化早已变得跟骑自行车一样简单。这归功于符合人体工程学的自动化软件系统,同时,经验丰富的自动化供应商提供了明确的流程使设置变得简单,包括参数编程。
必须明确一点,自动化定会改变车间内的一切。因其精湛的人体工程学设计,,自动化彻底改变了操作人员的作业内容和模式,同时也为职业发展创造了更佳的机遇。我们荷兰的客户便是很好的一则实例。在这家公司里,一个操作工承担了自动化的启动和运行,用了Fastems的系统多年后便成长为整个工厂的制造经理。自动化并非望尘莫及,只是与众不同。
在80年代,自动化系统的用户界面可能不是很友好,但自那以后,人体工程学和用户界面一直在改进。今天,任何制造商都可以使用自动化,且可以轻松上手。
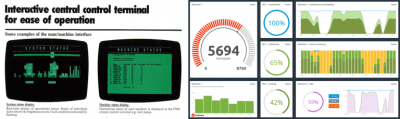
在80年代,自动化系统的用户界面可能不是很友好,但自那以后,人体工程学和用户界面一直在改进。今天,任何制造商都可以使用自动化,且可以轻松上手。
4. “自动化仅适合大型制造企业。”
该误解通常包括两个部分:技术和金钱。前者在文章第三点已经具体说明,因此在这里我们仅讨论金钱问题。在Fastems的客户中,即便是仅有2名员工的小作坊也能在自动化应用上获得可观的经济收益;中小型企业客户的年营业额可达到数百万欧元(或美元),并且只雇佣几十名员工。
经济可行的关键在于自动化的方案,不同的方案会导致不同的投资成本。今天的模块化解决方案大大降低了投资门槛。Fastems设计的入门级自动化系统,如FPC,具有高水平自动化功能,例如订单排产和资源掌控,并且在未来可以根据实际生产需求对系统进行扩展。这便是长久并且可持续的自动化投资。
在任何情况下,实现自动化关键的一点就是关注并愿意重新思考工艺,流程和工作方式——一种发展态度。幸运的是,大型和小型制造商都由这一共识!
5. “自动化的风险在于单点故障”
对此最常见的理解方式为:当我在生产中使用自动化,一旦某个生产节点出现故障,便会导致整个生产停摆;如果使用的仅为单机,节点故障只会导致这一台机床停摆,而不会影响到其他机床的生产,因此,独立单机系统抗错能力更强。
该如何打破这一错误的观点呢?这要看关注点,换句话说,我们应该将关注于年运行时间。比方说每年由于故障而导致的停产时间,并想尽一切办法减少停产,提高机床利用率,并结合交付时间与产品质量。
试想,若独立机器将具有100%的可用性和25%的年利用率;而自动化系统的可用性通常约为98%,机器利用率为60%,很明显在同样一年的时间内,后者是您的最佳投资选择。
此外,由于智能自动化解决方案带来了生产过程的标准化和生产计划和资源管理的控制软件,它实际上帮助我们减少了许多典型的停产风险,例如:
- 资源缺失
- 装夹问题
- NC数控程序故障(例如错误程序或参数错误)
- 刀具对刀错误等